Did you know the type of THY Precision Injection Molding Machine Types you pick can greatly affect the cleanliness of your medical or pharmaceutical parts? In cleanroom manufacturing, where a single particle can cause big problems, choosing the right machine is key. But what makes one machine better for cleanrooms than another? Let’s explore the differences in injection molding machine types and how to make your cleanroom operations better.
Key Takeaways
- Certain Injection Molding Machine Types are better suited for cleanroom environments than others.
- Understanding the differences between electric and hydraulic Injection Molding Machine Types is crucial for optimizing cleanroom operations.
- Cleanroom classifications and air filtration systems play a vital role in maintaining a sterile manufacturing environment.
- Positive and negative pressure cleanrooms offer unique advantages and require specialized auxiliary equipment.
- Careful consideration of cleanroom design and layout is essential for maximizing efficiency and controlling contamination.
Injection Molding Machine Types in Clean Room Manufacturing
In clean room manufacturing, the type of Injection Molding Machine Types is key to keeping the environment clean. THY Precision makes high-precision machines for these settings. They know how important it is to pick the right machine for clean rooms.
Electric vs. Hydraulic Injection Molding Machine Types
In clean rooms, electric machines are often chosen over hydraulic ones. Electric machines have fewer parts like motors and gears, which means less chance of dust. Hydraulic machines, however, have many parts like hoses and valves that could be sources of dust.
So, electric machines are better for clean rooms because they don’t bring in as much dust. THY Precision’s electric machines are made to keep the clean room dust-free, ensuring top-quality products.
Injectionmoldingmachinetypes | Advantages in Clean Room | Disadvantages in Clean Room |
---|---|---|
Electric |
|
|
Hydraulic |
|
|
Choosing between electric and hydraulic machines for clean room manufacturing is a big decision. THY Precision helps customers make the right choice for their clean rooms and goals.
Cleanroom Classifications and Air Filtration
At THY Precision, we know how crucial a clean environment is for our work. Our cleanrooms are made to keep the air free of dust and other particles. This ensures our products are top-notch for our customers. We follow international standards for cleanliness, with Class 1 being the strictest and Class 9 the least.
We use top-notch air filters to keep our cleanrooms spotless. HEPA or ULPA filters catch dust, germs, and other tiny particles in the air. The MERV rating of these filters shows how well they can trap different sizes of contaminants.
HEPA vs. ULPA Filters: Ensuring Optimal Air Purity
HEPA filters can remove 99.97% of particles 0.3 microns or bigger. ULPA filters catch 99.999% of particles 0.12 microns or bigger. We pick between HEPA and ULPA filters for our cleanrooms based on what each project needs. This ensures the air is super clean and free from contaminants.
- HEPA filters are used in Class 7 and Class 8 cleanrooms, which are perfect for most injection molding work.
- ULPA filters are used in the strictest Class 1 to Class 6 cleanrooms, where nothing but the cleanest air will do.
By focusing on cleanrooms and air filters, THY Precision makes sure our molding meets the toughest quality and cleanliness standards.

“Cleanroom air filtration is key to our quality control at THY Precision. We use the latest HEPA and ULPA tech to give our clients the purest products possible.”
Positive vs. Negative Pressure Cleanrooms
Choosing between injection molding machine types in clean room manufacturing is key. Positive pressure cleanrooms have more air pressure than outside. Negative pressure cleanrooms have less air pressure than outside.
Positive pressure cleanrooms keep contaminants out. Clean, filtered air flows outward, keeping the room clean. This is great for protecting products or processes from pollution.
Negative pressure cleanrooms are better for keeping contaminants inside. They make sure cleanroom air flow stays within the room. This helps prevent contaminants from escaping.
The choice between positive pressure cleanrooms and negative pressure cleanrooms depends on the injection molding machine types and processes. Both have their benefits. It’s important to pick the right one for the job.
“The choice between positive and negative pressure cleanrooms is a delicate balance, as each option offers distinct advantages depending on the unique needs of the manufacturing process.”
Auxiliary Equipment for Injection Molding Machine Types in Cleanrooms
Working with injection molding machines in a cleanroom means you need special equipment to keep things clean. THY Precision leads in injection molding tech. They know how important it is to manage cleanroom equipment well to make top-quality products without contamination.
One key piece of equipment is the material drying system. It removes moisture from raw materials like resins before they go into the machine. THY Precision keeps this system outside the cleanroom to avoid contamination.
The chiller equipment that cools the machine is also outside the cleanroom. Only the chiller’s water pipes go inside, keeping the air clean while cooling the machine.
Getting resin into the machine is another important step. THY Precision uses overhead pipes to bring in raw materials from outside. This cuts down on the chance of contamination.
Auxiliary Equipment | Location | Purpose |
---|---|---|
Material Drying System | Outside Cleanroom | Removes moisture from raw materials before injection |
Chiller Equipment | Outside Cleanroom | Cools the injection molding machine |
Resin Feeding System | Outside Cleanroom | Transports raw materials directly into the injection molding machine |
THY Precision places and manages these systems carefully. This way, the machines in the cleanroom work in a controlled, clean space. It helps make high-quality, precise parts.
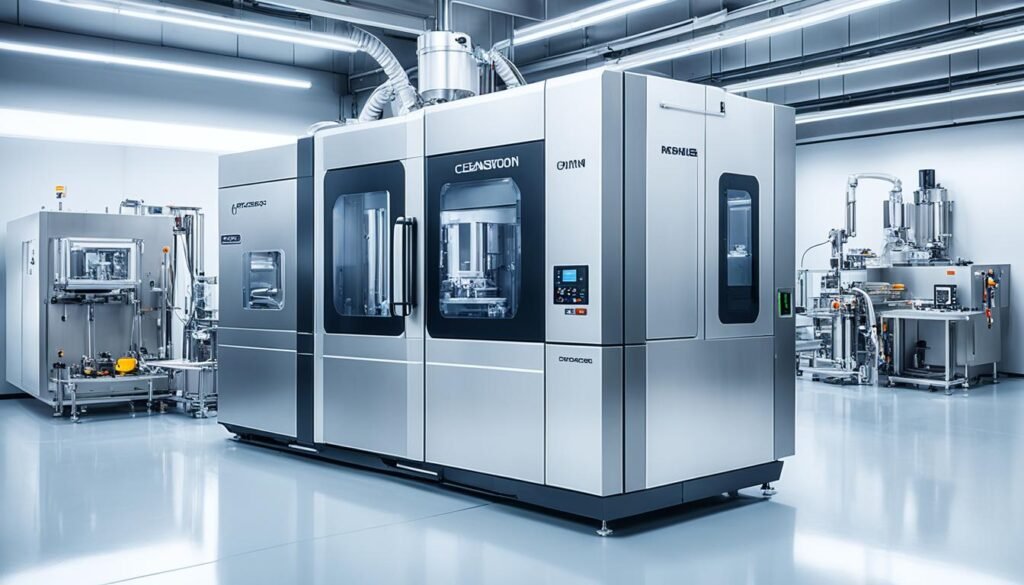
“Keeping the cleanroom clean is key to our success. At THY Precision, we focus on designing equipment that supports our quality and precision goals.”
Cleanroom Design Considerations
Creating a cleanroom for injection molding machines needs careful planning. The cleanroom design, layout, and airflow are key to keeping the air clean. This is vital for making products without contamination.
Managing airflow is a big part of cleanroom design for injection molding. The airflow must remove dust to keep the production area clean. HEPA or ULPA filters are used to clean the air to the right level.
Keeping the temperature and humidity right is also crucial. This helps the machines work well and keeps the products quality high. Smart systems are used to keep the environment at the right levels.
The cleanroom layout must help the workflow and reduce contamination risks. Where machines, tools, and people go is planned carefully. This makes the production area efficient and safe.
By focusing on these cleanroom design aspects, THY Precision keeps its injection molding top-notch. It ensures cleanliness, temperature, and humidity control. This leads to consistent, high-quality products for customers.
“Optimal cleanroom design is the foundation for successful injection molding in critical manufacturing environments.”
Conclusion
Injection molding cleanrooms are key for making high-quality, sterile plastic parts. They are used in medical, pharmaceutical, and aerospace industries. Knowing about injectionmoldingmachinetypes, cleanroom types, air filters, pressure control, and other equipment helps manufacturers make better products.
Designing the injectionmoldingmachinetypes layout and controlling airflow, temperature, and humidity is crucial. This keeps the cleanroom clean and controls contamination. THY Precision knows how to make cleanroom processes better. This can increase efficiency, cut costs, and give great results for your customers.
Working with THY Precision means using our deep knowledge of injection molding cleanrooms and our drive for innovation. We can help you improve your injectionmoldingmachinetypes and make sure your cleanroom operations succeed.